Behind the innovations: Sergio Corbera, director del Área del Automóvil y Mecánica de la Universidad Nebrija.
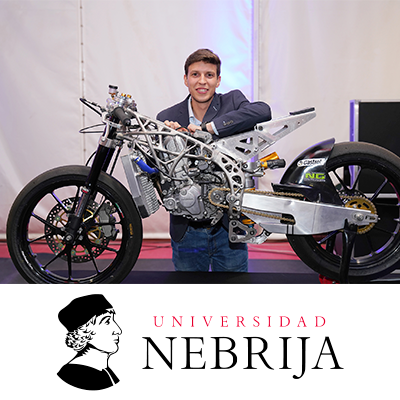
Advanced Manufacturing Madrid – ¿Cuál fue la motivación para empezar a desarrollar el proyecto de imprimir en 3D un chasis de acero?
Sergio Corbera – El acero es un material extraordinariamente versátil que presenta muchas ventajas; entre ellas, sus propiedades mecánicas. No obstante, su uso en ciertas aplicaciones en las que el peso puede ser un elemento crítico puede llegar a conferirle una posición inicial de desventaja. Conseguir que componentes de acero llegasen a ser igual de pesados o incluso más ligeros que los de aluminio y titanio, con unos costes controlados fue la principal motivación del proyecto. Dentro de este contexto, gracias a la experiencia del equipo de la Universidad Nebrija en el mundo del Motorsport, se consideró que el desarrollo de un chasis de moto en acero, aplicando fabricación aditiva representaba un reto de gran dimensión y relevancia para el proyecto.
Por lo general, el material más extendido en el mundo de las motos es el aluminio, con alguna excepción en acero. Características como la ligereza y ciertas propiedades que, tras años de investigación, proporcionan un buen comportamiento a la moto, han sido factores clave para que este material se haya convertido en un denominador común en cualquier chasis. Conseguir este mismo componente en acero que transmita unas sensaciones de conducción y rendimiento similares es uno de los hitos logrados por esta alianza entre ArcelorMittal y Nebrija.
AMM – ¿Cómo surgió la oportunidad de colaborar con AcerlorMittal?
S. Corbera – Arcelor-Mittal dispone de un centro de innovación tecnológica orientado al desarrollo de varias tecnologías punteras: impresión 3D, inteligencia artificial, nanotecnología y energía verde. La Universidad Nebrija integra las técnicas de inteligencia artificial y modelos generativos -diseño inteligente o diseño generativo- para conseguir desarrollar productos innovadores en el sector de la automoción. La impresión 3D y el desarrollo de algoritmos de diseño generativo están muy estrechamente relacionados, por lo que se consideró que de la colaboración de ambas partes podrían conseguirse productos de alto valor añadido. La relación se inició con el chasis de la moto, pero se ha convertido actualmente en toda una línea de desarrollo de alto impacto tecnológico que busca el desarrollo de nuevos productos innovadores.
AMM – ¿Nos puedes contar cómo fue el proceso de desarrollo del proyecto? ¿Alguna anécdota o piedra que se interpuso en el camino?
S. Corbera – El desarrollo de proyecto comienza acotando las condiciones de contorno del chasis, estableciendo los objetivos a conseguir, integración en la moto, volúmenes de control, etc. Comienza todo con un folio en blanco en el que se plasman todas estos aspectos y se genera el volumen de partida del que nacerá el chasis. A partir de este punto, en una primera instancia se generaron distintas opciones geométricas de chasis haciendo uso de la optimización topológica integrada en los software comerciales como ALTAIR, ANSYS y PARAMETERS. Estas geometrías iniciales no cumplían todos los condicionantes establecidos por la complejidad de los mismos. Actuaron como semillas geométricas que posteriormente fueron evolucionadas y optimizadas por los algoritmos desarrollados en la Universidad Nebrija, principalmente algoritmos evolutivos. Estos algoritmos fueron combinando las distintas soluciones geométricas y haciendo evoluciones geométricas para conseguir cumplir con todos los requisitos y requerimientos. Aspectos como ángulos de impresión, cantidad de soportes, balance de rigidez y pesos son algunos de los condicionantes introducimos en los algoritmos. Una vez obtenida la forma geométrica, desde el equipo de R&D de ArcelorMittal se comenzó a evaluar la viabilidad del proceso de impresión: estabilidad, disipación térmica, particiones, modificaciones geométricas, etc. Esta fase de hacer que el diseño óptimo pueda ser fabricado sin problemas es una tarea ardua en la que ArcelorMittal tuvo que volcar muchos recursos. Problemas no hubo como tal, pero sí que en un proceso tan complejo surgen complicaciones que pueden poner en riesgo el objetivo final. El chasis tiene espesores muy pequeños por lo que uno de los puntos más críticos era confirmar que durante el proceso de impresión no se produjese ningún problema. La deformación inherente a la geometría debido a la temperatura durante el proceso de impresión era otras de las incógnitas que podía generar complicaciones. La presencia de poros o pequeñas grietas. Todos ellos fueron pasos críticos que se fueron pudiendo evaluar y solucionar a medida que el proceso avanzaba. Son aspectos muy difíciles de controlar a priori ya que no se había hecho una pieza tan grande y compleja, por lo que toda este know-how adquirido es ya un éxito para la colaboración.
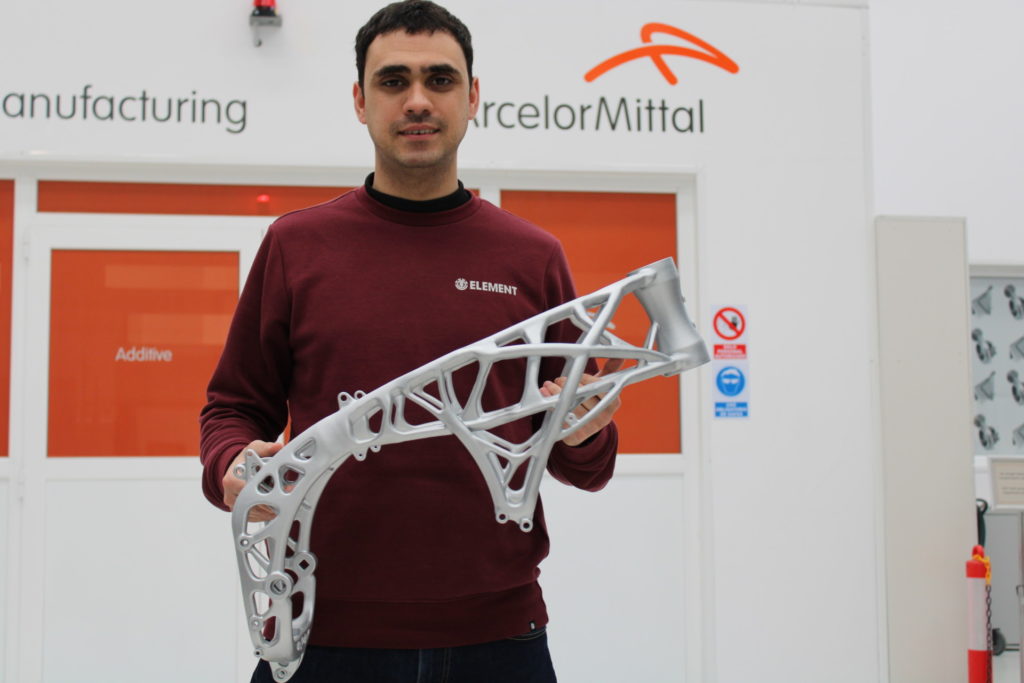
AMM – ¿Cuál es la tecnología que hay detrás del proyecto?
S. Corbera – El proyecto combina dos áreas muy innovadoras y que se encuentran en pleno auge: la fabricación aditiva y el diseño generativo. La primera de ellas era gobernada por ArcelorMittal y se hizo uso de sus instalaciones y sofisticadas tecnologías de impresión 3D. El chasis fue fabricado mediante la tecnología Selective Laser Melting (SLM), una de las más conocidas en este sector. En cuanto a la fase de diseño generativo, se hizo uso de algoritmos de optimización topológica y algoritmos evolutivos para toda la generación de las formas geométricas del chasis.
AMM – ¿Cuáles son las principales ventajas que ofrece este proyecto? ¿Qué necesidades cubre y cómo puede mejorar la vida de las empresas o equipos deportivos?
S. Corbera – Si nos centramos únicamente en el desarrollo del chasis, la principal ventaja viene asociada a la libertad de formas geométricas que permite la fabricación aditiva. Este tecnología abre el camino a explotar todo el potencial de técnicas de diseño gobernadas por algoritmos inteligentes. La capacidad de estos algoritmos a la hora de explorar el espacio de diseño ha permitido alcanzar un balance de rigidez del chasis óptimo (aspecto muy importante para el feeling del piloto), con un peso reducido y con una geometría innovadora. En este sentido, la libertad geométrica del proceso de fabricación junto con el potencial de las técnicas de diseño inteligentes permiten obtener productos que se aproximen más al óptimo buscado por los ingenieros, ya sea en términos de performance, peso o costes. Otro de los puntos angulares del proceso fue la posibilidad de desarrollar el chasis hueco con espesores de 0.8-1 mm de pared. Esto implicaba abordar varias cuestiones delicadas dentro de la fabricación aditiva: estabilidad de la pieza durante el proceso de impresión como consecuencia de los espesores tan reducidos; control de porosidades y propiedades mecánicas en esos espesores; y orientación de la forma geométrica para evitar soportes internos. Estás incógnitas se fueron resolviendo a lo largo del proceso de investigación gracias a ciertas propiedades que aporta el acero en el proceso de impresión y que posibilitaron que la realización de piezas huecas sea
AMM – ¿Cuáles son los próximos pasos de este proyecto?
S. Corbera – Los siguientes pasos del proyecto son su validación en condiciones reales, dentro de un circuito. Estamos iniciando una fase de test progresiva para ir confirmando la respuesta del chasis. Al ser impreso en 3D hay varias incertidumbres que debemos acotar y confirmar. Como responde a un impacto fuerte, el feeling que le transmite al piloto en curvas de baja/media y alta velocidad, su integridad estructural a lo largo del tiempo son algunas de ellas. Todas se han evaluado previamente por medio de simulaciones, pero siempre existe un gap entre simulación y realidad que es el que tenemos que terminar de acotar durante esta fase. El programa de test se compone de distintas fases, comenzando a baja velocidad y en circuitos pequeños para posteriormente ir a condiciones mucho más exigentes hasta finalmente validar el chasis para un campeonato completo. El objetivo es poder confirmar que esta tecnología es factible para el desarrollo de futuros componentes de motos y coches bajo las mismas premisas de seguridad y performance que los diseñados con las técnicas tradicionales.
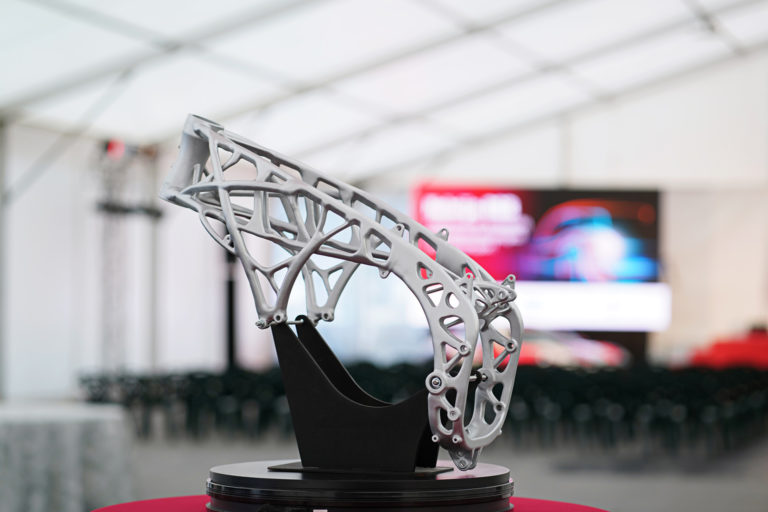
Suscríbete a nuestra newsletter
Crisis de talento: más del 60% de la industria no encuentra mano de obra cualificada
El último estudio realizado por Easyfairs, organizador de la feria líder del sector industrial Advanced Manufacturing, ha revelado que el mayor desafío para el 60,2%
¡No se pierda lo último en tecnología de soldadura y tratamientos de acero inoxidable!
Si busca innovación y eficiencia para su soldadura industrial, Soldaman tiene lo que necesita. Somos expertos en la venta de máquinas de soldar de alto rendimiento, diseñadas
Behind the inspirations: Conxita Domínguez
Simuladores MBSE y gemelos digitales. Mantenimiento Predictivo y Ciudades Inteligentes. Advanced Manufacturing Madrid – Cuéntanos un poco sobre tu historia, ¿cómo empezaste a trabajar en
Modula ofrece una alternativa eficaz para optimizar la logística interna y aumentar la productividad
Las empresas del sector del metal (fabricación, mecanizado o procesamiento) enfrentan desafíos únicos en la manipulación de materiales pesados y voluminosos. Las soluciones de almacenen