Behind the innovations: EUROCONTROL
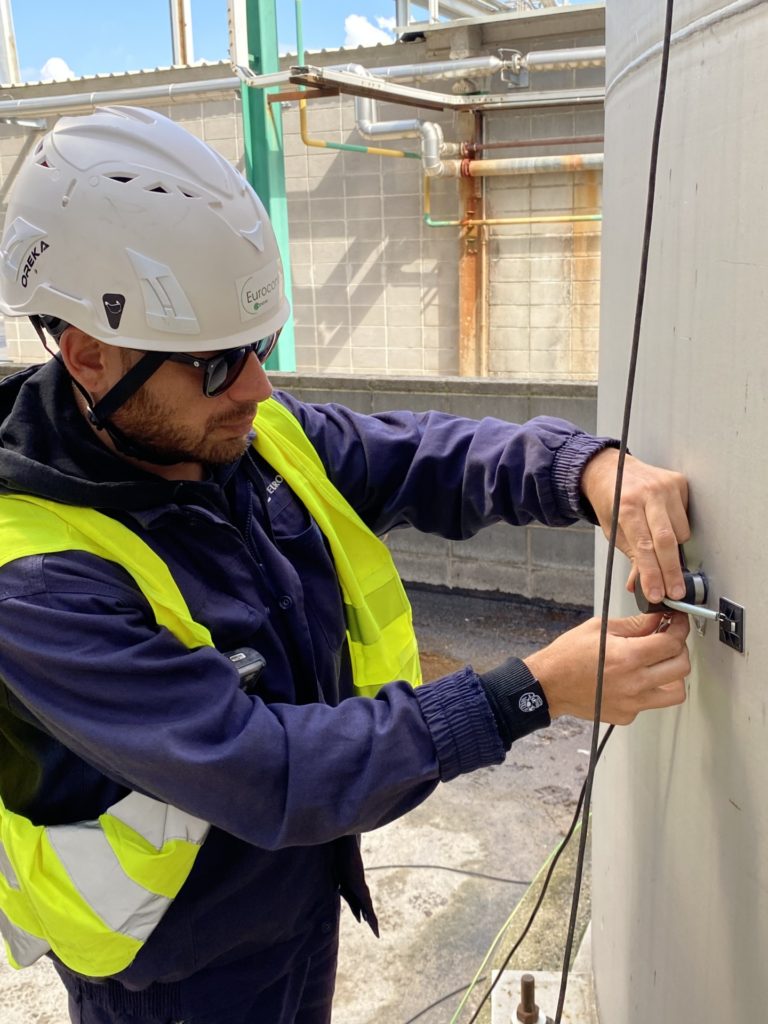
AMM – ¿Cuál fue la motivación para empezar a desarrollar este producto?
José Manuel Esteban, director de calidad de Eurocontrol –
En Eurocontrol llevamos más de 50 años evaluando la conformidad de las instalaciones y equipos regulados dentro del ámbito de la seguridad industrial: instalaciones y equipos destinados al almacenamiento de combustibles gaseosos, almacenamiento de productos químicos, productos petrolíferos, equipos a presión, protección contra incendios, etc.
Entre otros muchos parámetros de comprobación y ensayo, la legislación que aplica a estas instalaciones establece habitualmente la realización de pruebas de estanquidad y de resistencia mediante el empleo de agua como fluido de ensayo y de una inspección visual interior para comprobar la adecuación y ausencia de defectos en tanques de almacenamiento, tuberías de distribución, etc.
Sin embargo, la experiencia nos ha permitido comprobar que esta metodología de ensayo no evoluciona con las nuevas tecnologías, no siempre es la más adecuada, e incluso puede suponer un perjuicio para la propia instalación, el personal de mantenimiento e inspección y el medio ambiente.
Perjuicios para la instalación
La existencia de numerosos productos incompatibles con el agua implica que la evaluación de los recipientes que los contienen requiera la realización de un vaciado, lavado, prueba de presión/estanqueidad y un riguroso secado posterior que
garantice la seguridad de la instalación una vez puesta en marcha de nuevo.
Perjuicios para el personal de mantenimiento e inspección
Para realizar la inspección visual interior, el personal inspector y de mantenimiento debe entrar en los tanques de almacenamiento, lo que supone que el trabajo se realiza en un espacio confinado y existe un riesgo derivado de contactos químicos, atmósferas explosivas, trabajos en altura, etc.
Perjuicios para el medio ambiente
La secuencia de procesos necesarios para la realización de las pruebas hidráulicas y de estanqueidad conlleva la generación de un altísimo volumen de agua contaminada que requiere un tratamiento posterior.
Por último, en Eurocontrol somos plenamente conscientes de la repercusión económica que implica para los titulares de las instalaciones no solo garantizar el cumplimiento reglamentario, sino sobre todo paralizar los procesos de fabricación durante el tiempo que requiere la revisión e inspección de los sistemas.
Estas razones han sido las principales motivaciones que han llevado a equipo de dirección de Eurocontrol a desarrollar este producto.
2. ¿Nos puedes contar cómo fue el proceso de desarrollo del producto? ¿Alguna anécdota o piedra que se interpuso en el camino?
Para el desarrollo del producto hemos trabajado en torno a cuatro ejes principales:
- Evaluación normativa en materia de seguridad industrial: nuestros expertos en seguridad evaluaron los requisitos normativos de ámbito europeo, nacional y autonómico para analizar el alcance, la periodicidad y las metodologías establecidas en cada documento normativo y las posibilidades de reconocimiento e implantación de nuevas tecnologías para su ejecución.
- Evaluación de técnicas avanzadas de ensayos no destructivos (END): nuestros expertos Nivel 3 investigaron las técnicas avanzadas de ensayos no destructivos existentes en el mercado que pudieran dar soluciones a los perjuicios y problemas identificados. En este sentido, desde el inicio el estudio se centró en la técnica de ensayo basada en emisión acústica. Esta técnica de ensayo, en la que somos especialistas, fue implantada por primera vez en España por Eurocontrol en el sector gasista, hace aproximadamente 15 años.
Durante el proceso, nuestros técnicos Nivel 2 y 3 analizaron los métodos y estándares de ensayo en el ámbito europeo, con el objetivo de localizar aquellos que pudieran garantizar la monitorización de los tanques de almacenamiento para evaluar la estanqueidad y ausencia de defectos (principalmente, fuente de corrosión) desde el exterior y sin vaciar el tanque de producto.
- Prueba en instalaciones de almacenamiento: prueba, desarrollo y validación del método de ensayo sobre instalaciones de almacenamiento existentes. La amplia variación de instalaciones en función de su altura, diámetro, material, configuraciones, soportaciones, calorifugado, existencia de sistemas de agitado, sistemas de calefacción, etc., supuso un reto importante para el equipo de expertos a la hora de monitorizar las estructuras sin considerar fuentes de emisión ajenas a ella.
- Establecimiento del marco legal necesario para reconocer el nuevo método dentro del marco normativo:
Para garantizar el reconocimiento del método y que pudiera ser considerado como solución técnica alternativa a la prueba hidráulica, la dirección técnica de Eurocontrol ha formalizado múltiples procesos administrativos, entre los que destacamos:
- Presentación y supervisión in situ de los ensayos finales a los responsables en materia de seguridad industrial de las Direcciones Generales de Industria de varias comunidades Autónomas.
- Obtención de la acreditación ENAC como laboratorio de ensayo por emisión acústica en los métodos y normas de ensayos requeridos y aprobados.
Dentro de esta fase nos hemos encontrado con las principales dificultades y máximas exigencias del desarrollo del producto.
Como anécdota, podemos mencionar que la supervisión de uno de los responsables del departamento de Industria de una comunidad autónoma (cuyo nombre preferimos no desvelar) se produjo, de forma inesperada, durante unas pruebas de validación del método en las instalaciones industriales de un cliente pleno mes de agosto. A pesar de que los ensayos y la presentación se llevaron a cabo en unas condiciones ciertamente poco idóneas y no previstas (temperatura extrema, alta humedad, altas exigencias en EPIS, etc.) finalmente fueron un éxito, tanto en el desarrollo como en la aprobación final.
3. ¿Cuál es la tecnología que hay detrás de esta innovación?
Detrás de la innovación está la tecnología de ensayos no destructivos avanzada llamada emisión acústica.
Frente a otras técnicas de ensayos no destructivos, la técnica de emisión acústica presenta la ventaja de monitorizar toda la estructura de una sola vez, evaluando la presencia de posibles imperfecciones y su evolución, tanto en equipos sometidos a presión como atmosféricos. La evaluación de la integridad del depósito mediante este método constituye un ensayo no destructivo volumétrico y global utilizado a nivel nacional e internacional con éxito desde hace varias décadas.
Diferentes factores evidencian la alta validez, fiabilidad y seguridad del método propuesto: el avance tecnológico, los equipos de ensayo de última tecnología, la normativa técnica específica que estandariza la ejecución de los ensayos y la existencia de una certificación para el personal que ha de realizarlos bajo el estándar ISO 9712, así como la acreditación ENAC de los laboratorios que llevan a cabo los ensayos según norma UNE-EN ISO/IEC 17025.
En este sentido, debemos destacar que Eurocontrol fue el primer laboratorio acreditado por ENAC bajo la UNE-EN ISO/IEC 17025 en la técnica de emisión acústica, hace más de diez años.
Los resultados obtenidos gracias a este tipo de ensayos ofrecen suficiente información para evaluar globalmente el estado de conservación del equipo ensayado, tanto de la superficie interior como exterior. Igualmente, ofrecen información sobre la estanquidad del equipo con una tasa de fuga muy superior al “pasa” o “no pasa” establecido en las pruebas tradicionales (hidrostática y/o estanquidad).
La capacidad que tienen todos los materiales para producir y propagar, a través de su estructura, fuentes de emisión acústica producidas por la evolución de cualquier tipología de defectos (corrosiones, fisuras, etc.) hace que la colocación estratégica de sensores piezoeléctricos a lo largo de la estructura ensayada permita monitorizar, registrar y analizar/evaluar en tiempo real las señales recibidas y, por tanto, su criticidad. En este sentido, en función de las normas de ensayo empleadas, la configuración triangular de sensores instalados permite no sólo la identificación de las fuentes emitidas sino incluso su localización sobre la estructura. De esta manera, tras identificar la zona del equipo en la que se localizan los defectos, se pueden utilizar otras técnicas de ensayos no destructivos cuantitativas para dimensionar el defecto identificado (ultrasonidos, líquidos penetrantes, etc.).
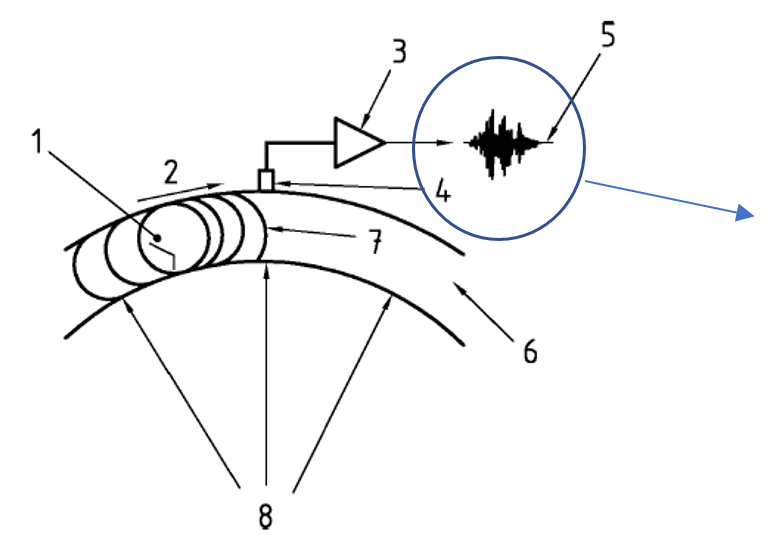
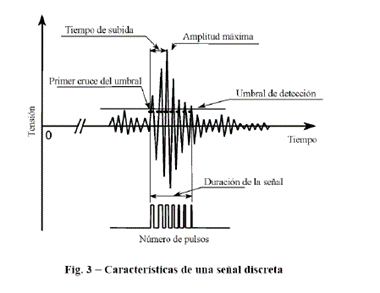
Suscríbete a nuestra newsletter
Crisis de talento: más del 60% de la industria no encuentra mano de obra cualificada
El último estudio realizado por Easyfairs, organizador de la feria líder del sector industrial Advanced Manufacturing, ha revelado que el mayor desafío para el 60,2%
¡No se pierda lo último en tecnología de soldadura y tratamientos de acero inoxidable!
Si busca innovación y eficiencia para su soldadura industrial, Soldaman tiene lo que necesita. Somos expertos en la venta de máquinas de soldar de alto rendimiento, diseñadas
Behind the inspirations: Conxita Domínguez
Simuladores MBSE y gemelos digitales. Mantenimiento Predictivo y Ciudades Inteligentes. Advanced Manufacturing Madrid – Cuéntanos un poco sobre tu historia, ¿cómo empezaste a trabajar en
Modula ofrece una alternativa eficaz para optimizar la logística interna y aumentar la productividad
Las empresas del sector del metal (fabricación, mecanizado o procesamiento) enfrentan desafíos únicos en la manipulación de materiales pesados y voluminosos. Las soluciones de almacenen
Por otro lado, el carácter no invasivo de la técnica posibilita realizar las pruebas en las condiciones de servicio del equipo y con el propio producto que lo contiene, lo que representa para el usuario un ahorro de tiempo y de “lucro cesante” respecto a las pruebas tradicionales. Asimismo, se evitan riesgos medioambientales, dado que es un ensayo en el que no se producen residuos que requieran un tratamiento posterior, como ocurre con las aguas usadas en pruebas hidráulicas, que generalmente quedan contaminadas por restos de los fluidos contenidos en los equipos durante su servicio.
Marco normativo de referencia respecto a la técnica de emisión acústica:
Normativa Nacional
- Norma UNE 60250, de obligado cumplimiento para depósitos de almacenamiento de GLP regulados por el RD 919/2006. Punto 10.4.
- ITC EP-03 Refinerías y Plantas Petroquímicas aprobado por el Reglamento de Equipos a Presión RD 809/2021
- Apartado 6.2.3.5.1 del Acuerdo para el transporte Internacional de Mercancías Peligrosas.
Normativa Internacional
- Francia: Guía AFIAP sobre ensayos de equipos a presión
- Portugal: Decreto Lei 131/2019 por el que se aprueba el reglamento de equipos a presión
- Italia: Procedimiento de inspección de depósitos de GLP aprobado por el ISPELS.
4. ¿Cuáles son las principales ventajas que ofrece este producto innovador? ¿Qué necesidades cubre y cómo puede mejorar la vida de las empresas?
Las principales ventajas que ofrece este ensayo respecto a las metodologías existentes son las siguientes:
- Mejor diagnóstico de la instalación
Tras las pruebas de estanquidad y de resistencia hidráulica se obtienen resultados del tipo “Pasa” “No pasa”, que no aportan información adicional sobre la estructura. Sin embargo, a través de la técnica de emisión acústica se monitoriza toda la actividad del equipo durante el ensayo, permitiendo evaluar su conformidad en base a múltiples parámetros adquiridos (amplitudes, energías, tiempos, etc.), registrados e incluso localizando las áreas críticas/emisoras para que posteriormente puedan ser evaluadas por otras técnicas cuantitativas avanzadas.
- Más seguridad para las personas
Su carácter no invasivo y de evaluación global permite conocer tanto la estanquidad del tanque como su estado interior, sin necesidad de acceder a su interior.
- Menor coste: menos tiempos de parada y de procesos asociados
Las inspecciones convencionales requieren parar la instalación, vaciarla de producto, limpiar la superficie interior, colocar estructuras de inspeccion visual interior, llenar de líquido, vaciar, secar y ponerla nuevamente en producción. En el ensayo por emisión acústica, los sensores se colocan en el exterior del tanque y la monitorización de su comportamiento se realiza sin vaciarlo. La instalación, por tanto, está menos tiempo fuera de servicio, lo que supone un ahorro considerable de los costes asociados a los procesos de inspección y mantenimiento asumidos por el titular de las instalaciones.
- Mejor cuidado del Medio Ambiente
El titular reduce su impacto medioambiental al no requerir el tratamiento del agua contaminada obtenido como subproducto del ensayo de estanquidad de la estructura.
5. ¿A qué industrias está dirigida principalmente la innovación?
Este producto va dirigido principalmente a industrias químicas y farmacéuticas que producen almacenamientos de productos químicos regulados actualmente por el Real Decreto 656/2017.
6. ¿Cuáles son los principales obstáculos con los que se encuentra una empresa que quiere desarrollar un producto innovador?
Los principales obstáculos que se encuentra una empresa privada para el desarrollo de un producto innovador se derivan de la obtención de fuentes de financiación que permitan amortiguar los costes asumidos en su desarrollo.
Las empresas privadas normalmente centran sus objetivos estratégicos en satisfacer las necesidades de sus clientes, garantizando el cumplimiento de unos objetivos cualitativos, pero principalmente cuantitativos, es decir, un presupuesto. Por tanto, para potenciar las actividades de innovación y minimizar el riesgo económico asumido por los elevados costes de la tecnología empleada, la escasa disponibilidad de personal técnico experto y especializado, etc., es imprescindible facilitar al máximo a las empresas privadas alcanzar con éxito fuentes de financiación.
En Eurocontrol llevamos más de quince años desarrollando proyectos de investigación dentro del ámbito de inspección y ensayo e innovación tecnológica de nuestros procesos, lo que supone para la compañía una inversión anual que ronda los 0,8-1 M€. En este sentido, desde el departamento de innovación se trabaja muy intensamente en la obtención de diferentes ayudas, bien a través de financiación del CDTI (Centro para el Desarrollo Tecnológico y la Innovación), bien como deducciones fiscales, siempre bajo certificación del proyecto de investigación/innovación por entidades de certificación acreditadas por la Entidad Nacional de Acreditación (ENAC).
Síguenos en nuestras redes sociales
Compartir este artículo