AIMPLAS and TNO conclude that solvolysis is the best method for the recycling of biocomposites from the aeronautical sector.
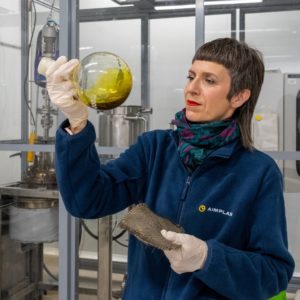
Throughout the study, 12 methods were analysed for six different biocomposites, with solvolysis and pyrolysis being the two most promising alternatives tested on a large scale in a pilot plant.
The results show that pyrolysis emits 17% more carbon dioxide and consumes twice as much heat as solvolysis.
The aviation industry is increasing the use of biocomposite materials in its components to mitigate its environmental impact. Biocomposites use natural fibres for reinforcement and resins from renewable sources. However, the novelty and heterogeneity of these materials, their thermosetting nature and the fact that they lack carbon fibres, which have a high market value, make it difficult to find an efficient solution for their management when they become waste at the end of their useful life.
AIMPLAS, Instituto Tecnológico del Plástico, and the Dutch centre TNO have completed the ELIOT project, which has enabled an in-depth review of the current recycling technologies for both composites and biocomposites used in the aeronautical sector to analyse the most technically feasible alternatives on a pilot plant scale that are viable from a technical and economic point of view. As a result of the study, solvolysis is presented as the best method among the 12 technologies analysed for the recycling of six different biocomposites.
This study contributes to promote cost-efficient recycling technologies that allow the aeronautical industry to guarantee the sustainability of its components in the search for new solutions aligned with the Circular Economy.
The results show that pyrolysis emits 17% more carbon dioxide and consumes twice as much heat as solvolysis, which implies a higher associated cost. Solvolysis uses solvents as a substitute for heat, but these are highly efficiently recovered and reused in the process. Moreover, solvolysis has been shown to work even better when the biocomposite is larger.
In both cases, pyrolysis and solvolysis, additional purification steps are required to utilise the pyrolytic liquid and the distilled product, respectively. Estimates have been made for a processing plant with a treatment capacity of 10 kilotons of biocomposite per year.
Other technologies analysed during the study were mechanical recycling, dissolution, enzymatic degradation, gasification and composting.
The ELIOT project has received funding from the European research and innovation programme Horizon 2020 in the framework of the Clean Sky Joint Technology Initiative and with funding agreement number 886416.
About AIMPLAS
At AIMPLAS we help companies to apply the Circular Economy to their business model in order to convert the legislative changes affecting the plastics industry into opportunities to improve their efficiency, reduce their environmental impact and increase their economic profitability. To this end, we work and research in areas such as recycling, biodegradable materials and products, the use of biomass and CO2, with the aim of developing innovative solutions to help solve current environmental challenges.
About TNO
The Netherlands Organisation for Applied Scientific Research (TNO) is an independent research organisation. We connect people and knowledge to create innovations that enhance the sustainable competitiveness of industry and the well-being of society. Now and in the future. Together with our partners, we focus on the societal challenges of a safe, healthy, sustainable and digital society. This is our mission and it is what drives us, the more than 4,600 TNO professionals, in our daily work.
Subscribe to our newsletter
¡Por un 2024 más industrial que nunca!
Stay informed Síguenos en nuestras redes sociales Facebook-f Twitter Instagram Linkedin Compartir este artículo
¡Enamórate de la innovación en Advanced Manufacturing News!
Stay informed Síguenos en nuestras redes sociales Facebook-f Twitter Instagram Linkedin Compartir este artículo
La diversidad aporta riqueza
Stay informed Síguenos en nuestras redes sociales Facebook-f Twitter Instagram Linkedin Compartir este artículo
En abril comienza el plazo para presentarte a los Advanced Manufacturing Awards
Stay informed Síguenos en nuestras redes sociales Facebook-f Twitter Instagram Linkedin Compartir este artículo