Functional integration: 3D printing of a metal injection moulding (MIM) tool with near-contour cooling
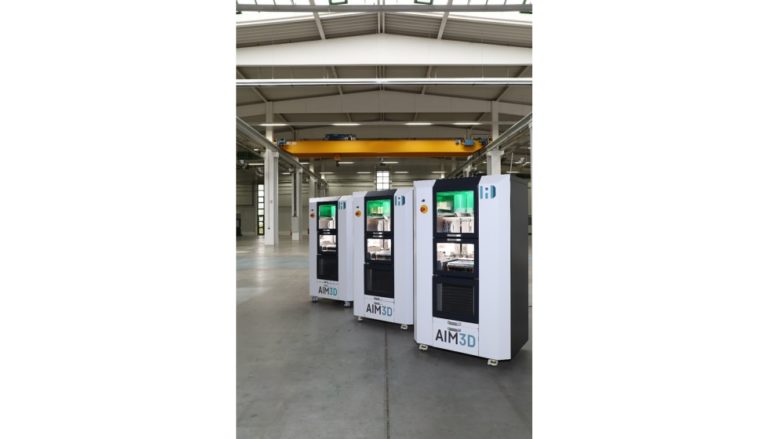
The Chair of Microfluidics at the University of Rostock is collaborating with Stenzel MIM Technik GmbH (Tiefenbronn, near Pforzheim) on a project to 3D print a metal injection moulding (MIM) tool. The basis of the development is the use of AIM3D’s EMC technology with an ExAM 255 system. The ExAM 255 system combines high 3D component accuracy with high build speeds for additive manufacturing (AM). Compared to a conventional machining approach, using an AM process to produce a MIM tool reduces the total production time from about 8 weeks to approximately 5 days.
As part of a project funded by the German Federal Ministry of Economics and Energy (BMWi), the 3D printed MIM tool is a cooperative development between the Chair of Microfluidics (LFM) at the University of Rostock and Stenzel MIM Technik GmbH. The duration of the project is from April 2021 to October 2023. The basis of the process and application is the use of AIM3D’s EMF technology, implemented in an ExAM 255 system. The project represents the current state of the art in metal 3D printing.
Stay informed
Último llamamiento para participar en la III edición de los Advanced Manufacturing Awards
Los galardones, impulsados por Easyfairs, premian los proyectos más innovadores, eficientes y sostenibles de la industria, seleccionados por un jurado de expertos y la votación
Easyfairs abre el registro para la 16º edición de Advanced Manufacturing Madrid
El evento referente en la industria regresa a la capital para mostrar las últimas novedades para la cadena de valor a través de sus tres
La Comunidad de Madrid desarrolla un gemelo digital para analizar en tiempo real la fabricación de materiales compuestos
La Comunidad de Madrid desarrolla un gemelo digital para analizar en tiempo real la fabricación de materiales compuestos La Comunidad de Madrid ha desarrollado un
Hyundai y Toray se unen para dar forma a una nueva era de movilidad a través de la innovación de materiales
Hyundai y Toray se unen para dar forma a una nueva era de movilidad a través de la innovación de materiales El proveedor japonés de