Behind the innovations: Atotech
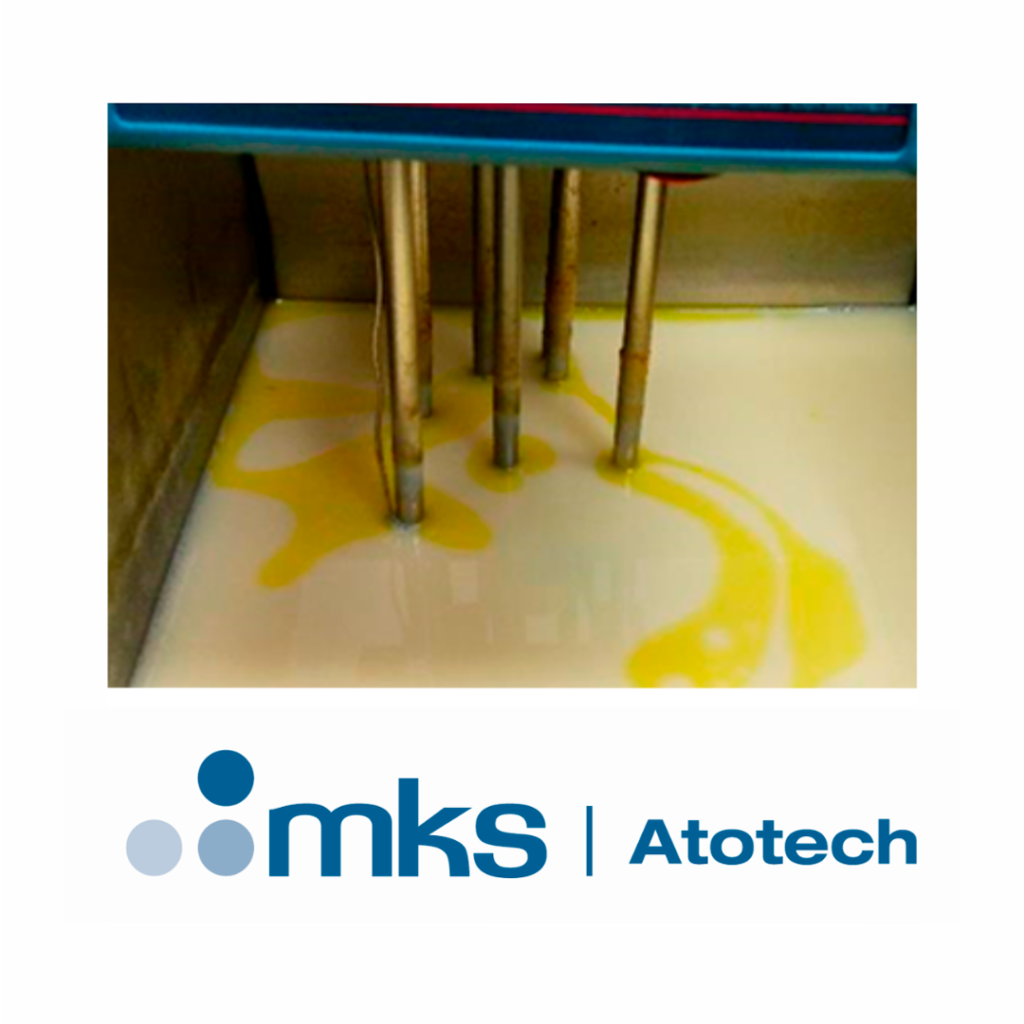
AMM – What was the motivation to start developing the Uniprep Long Life product?
Atotech – Over the last decade, we have focused significantly on making our Atotech product portfolio more environmentally friendly. We are committed to reducing the use of hazardous chemicals and are at the forefront of developing less harmful processes that go beyond industry standards. Our Atotech systems and equipment are designed to use water, energy and raw materials very efficiently, reusing and recycling wherever possible. To improve further, we have made sustainability a key driver of our R&D strategy. This approach also applies to our cleaning solutions portfolio, where we have focused on developing a product that works in a more sustainable way and therefore also results in economic benefits for the customer. In the metal finishing industry, you will find cleaning and degreasing processes from a large number of chemical suppliers. In general, the technology used and the operation can be quite similar. With a sustainable solution, we wanted to differentiate ourselves from the industry and leverage this to improve the customer experience.
AMM – Can you tell us about the product development process, any anecdotes or stumbling blocks that got in the way?
Atotech – UniPrep’s goal was to develop a long-lasting technology. Any development needs to be as thorough as possible to ensure the viability of the process. Consequently, the development process was lengthy to allow for lifetime studies of the technology. For example, to quantify the effectiveness of the long-life technology, a 10-week study was conducted to measure the change in organic matter. The attached diagrams show some of these capabilities.
AMM – What is the technology behind this innovation?
Atotech – The technology on which the UniPrep long-life system is based is patented, but in principle it supports the degradation of organic compounds that are introduced into the solution during the degreasing process. Typical organics we refer to include forming and stamping fluids, cutting fluids, coolants and the like, which are found in the metal finishing industry.
AMM – What are the main advantages of this innovative product, what needs does it cover and how can it improve the life of companies?
Atotech – The main advantage of the long-life technology is that it can help reduce waste. Think of a degreaser that has to be disposed of every month versus one that is only disposed of every three months. If the degreaser tank is 5,000 litres, one applicator can eliminate 40,000 litres of used chemicals that must be sent to wastewater treatment. This also helps to reduce the amount of chemical needed, as each new replenishment will require a certain amount to reach the required working concentration. In addition, for applicators who normally use some form of filtration or oil skimming, it can potentially eliminate the need for this and the secondary oil waste stream. In addition, this means that there are no equipment running and maintenance costs and staff can focus on other activities. All this can be achieved without compromising the quality of the final part.
The low temperature capabilities of UniPrep cleaners also offer additional advantages. By reducing the operating temperature of the cleaner compared to a conventional cleaner, applicators can see significant energy cost savings. This is especially important in today’s economy, where energy costs are rising rapidly. In turn, low energy consumption also has a direct correlation to the carbon footprint. With increasing scrutiny on carbon emissions, this is another unique added value possible with UniPrep cleaners.
AMM – Which sectors are you mainly targeting for innovation?
Atotech – architectural aluminium and furniture. In recent years, this technology has also been adopted for many coating applications, driven largely by the automotive market, but also with widespread adoption in the fastener industry.
AMM – What are the main obstacles facing a company that wants to develop an innovative product?
Atotech – There are many challenges a chemical supplier faces when developing new processes. The most difficult is to understand the needs or demands of the market or the customer, be they technical, commercial or environmental, and turn them into a viable solution. It is absolutely critical to be in tune with current market requirements and to anticipate what may come in the future; otherwise, developments solve today’s problems while missing features that would make them a sustainable solution for many years to come.
Subscribe to our newsletter
Último llamamiento para participar en la III edición de los Advanced Manufacturing Awards
Los galardones, impulsados por Easyfairs, premian los proyectos más innovadores, eficientes y sostenibles de la industria, seleccionados por un jurado de expertos y la votación
Easyfairs abre el registro para la 16º edición de Advanced Manufacturing Madrid
El evento referente en la industria regresa a la capital para mostrar las últimas novedades para la cadena de valor a través de sus tres
La Comunidad de Madrid desarrolla un gemelo digital para analizar en tiempo real la fabricación de materiales compuestos
La Comunidad de Madrid desarrolla un gemelo digital para analizar en tiempo real la fabricación de materiales compuestos La Comunidad de Madrid ha desarrollado un
Hyundai y Toray se unen para dar forma a una nueva era de movilidad a través de la innovación de materiales
Hyundai y Toray se unen para dar forma a una nueva era de movilidad a través de la innovación de materiales El proveedor japonés de