Apply cutting power machining strategies to maintain productivity.
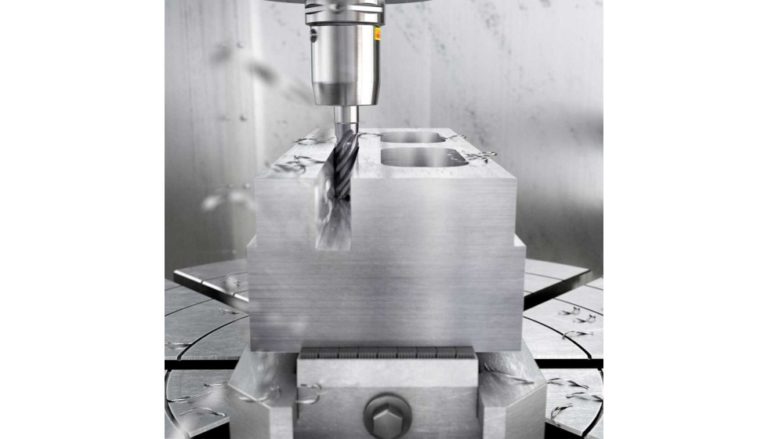
Machine shops are always looking to increase productivity, improve efficiency and reduce costs driven by market demands and the constant drive to remain competitive. Roughing end mills are one solution to these needs, but many of the tools available on the market have performance limitations, both in tool life, productivity and process safety. This article explains how the CoroMill Plura HD integral carbide slotting end mill can overcome these shortcomings, with more predictable and reliable performance.
The Financial Times has identified inflation and the war in Ukraine as the main factors driving up energy and raw material prices, including steel. These cost increases pose a major obstacle for manufacturers in achieving a low cost per part, as well as having a direct impact on manufacturers’ profitability. How can manufacturers overcome these obstacles in their machining applications, while meeting market demands and remaining competitive?
One solution is to apply a cutting power machining strategy, which has proven to be a very effective approach to roughing operations. Such a strategy ensures efficient chip removal rates and excellent process safety. With an effective cutting power strategy, manufacturers can optimize roughing operations, increasing productivity and reducing cycle times.
But how should a cutting power strategy be implemented? Simply put, the method is similar to high feed side milling (HFSM) but with a larger radial cutting width, and only benefits from controlled fogging and tool loading. To apply it successfully, the method requires constant high radial fogging and smooth movements during machining, which contributes to improved process safety, tool life and productivity.
Other strategies
Before discussing the cutting power strategy, let’s briefly examine two conventional options for roughing. First, there is the frame-frame strategy, an older roughing strategy with an inefficient tool path. Advantages of a frame-frame strategy include the lack of need to update NC programs and that the programs are small, which is beneficial for older machines with limited memory and processing capabilities. Disadvantages include not being able to use the full potential of the cutting tool in the ‘easy parts’ of the tool path, as well as overloading the cutting tool, for example, in corners. The result is poor in all aspects of machining performance (tool life, productivity, process safety, machined part quality and machine tool wear/maintenance).
Next, we come to the aforementioned HFSM strategy, an efficient, high-performance strategy that utilizes the full performance of the tool with high process reliability and tool life. HSFM tools typically have a very high tooth density, which is very beneficial for tool life as well as productivity when machining with small radial fogging. The small radial fogging also allows for a very high axial depth of cut. However, these tools are not at all suitable for larger radial fogging and, even if applied with a smaller axial depth of cut, they will break. If a double depth of cut (2×DC), or less, is required, the power cutting strategy is more effective.
However, to achieve this, tools designed for higher fogging are needed. So Sandvik Coromant engineers developed an optimized and efficient solid carbide end milling cutter that would excel in this field. The result was CoroMill Plura HD and now the next generation is launched with two new grades.
You can read more here:
Stay informed
Último llamamiento para participar en la III edición de los Advanced Manufacturing Awards
Los galardones, impulsados por Easyfairs, premian los proyectos más innovadores, eficientes y sostenibles de la industria, seleccionados por un jurado de expertos y la votación
Easyfairs abre el registro para la 16º edición de Advanced Manufacturing Madrid
El evento referente en la industria regresa a la capital para mostrar las últimas novedades para la cadena de valor a través de sus tres
La Comunidad de Madrid desarrolla un gemelo digital para analizar en tiempo real la fabricación de materiales compuestos
La Comunidad de Madrid desarrolla un gemelo digital para analizar en tiempo real la fabricación de materiales compuestos La Comunidad de Madrid ha desarrollado un
Hyundai y Toray se unen para dar forma a una nueva era de movilidad a través de la innovación de materiales
Hyundai y Toray se unen para dar forma a una nueva era de movilidad a través de la innovación de materiales El proveedor japonés de